Acerca de

ENHANCED OIL
RECOVERY
ENHANCED OIL RECOVERY (EOR)
Enhanced Oil Recovery (EOR) represents a critical advancement in the energy sector, enabling the extraction of oil that traditional methods leave behind. By utilizing innovative techniques such as gas injection, chemical flooding, and thermal recovery, EOR significantly boosts oil recovery rates, extending the productive life of reservoirs. These methods not only improve efficiency but also help maximize the return on investment in oilfield operations. As global demand for energy persists and easily accessible reserves diminish, EOR technologies such as Paulsson's Fiber Optic Vector Sensor (FOSVS™) and geophones play a pivotal role in meeting energy needs while reducing the environmental footprint of oil production through better resource management.


FOSVS AND GEOPHONES FOR EOR
FOSVS™ measure acceleration at sub-micro Joule energies to over 10,000 Hz at 320°C. FOSVS™ have been developed by Paulsson under Department of Energy (DOE) funding for micro-seismic and high temperature applications.
Geophones are devices that are commonly used in seismic exploration to detect vibrations or seismic waves in the subsurface. They are used for mapping oil and gas reservoirs and monitoring primary and enhanced hydrocarbon recovery.
During enhanced hydrocarbon recovery, fluids are injected into the reservoir to increase the pressure and move the oil or gas towards the production wells. FOSVS™and geophones are used to monitor the effectiveness of this process by detecting the small micro-seismic events generated by the fluid injection.
When fluids are injected into the reservoir, it causes rocks to fracture which generates micro-seismic events. These events can be detected by FOSVS™ and geophones placed within the reservoir. The data from our sensors are used to create 3D/4D images of the reservoir and to monitor the movement of the fluids.
By analyzing the data, engineers can determine how the fluids flow through the reservoir and make adjustments to the process to optimize injection and production. They can also identify areas untouched by the fluids inside the reservoir and target those areas for additional injection.
Overall, the use of Paulsson's technologies for enhanced hydrocarbon recovery will greatly improve the efficiency of oil and gas production and reduce costs by providing real-time monitoring of the injection process.
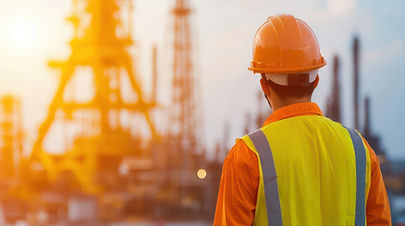
DEVELOPMENT AND PRODUCTION
Seismic, pressure, strain and temperature sensors are used to measure and analyze various physical properties of the earth's surface, and subsurface. The development and production of geophysical equipment involves the following steps:
Production
Once the equipment has passed the testing and calibration process, it can then be produced on a larger scale. The production process involves assembling the equipment, testing it, and then packaging it for shipping.
Testing and Calibration
The next step is to test and calibrate the equipment to ensure its functionality and accuracy in real-world conditions. This involves conducting a series of tests to verify that the equipment performs according to the required specifications, such as pressure, temperature, and flow rates. Any discrepancies found during testing are addressed through calibration adjustments to optimize performance and ensure the equipment operates reliably during the enhanced oil recovery process.
Prototype Development
After selecting the components, a prototype is developed. The prototype is used to test the functionality of the equipment and to determine if any design modifications are required.
Component Selection
Once the design is finalized, the next step is to select the required components. This includes sensors, data loggers, processors, power supplies, and other ancillary components needed to operate the equipment.
Conceptualization and Design
The next step is to conceptualize the equipment and its design. This involves determining the physical properties to be measured and the necessary hardware and software components needed for measurement and data analysis.
Quality Control
Throughout the production process, stringent quality control measures are implemented at each stage to ensure that every piece of equipment adheres to the necessary performance and safety standards. These measures involve continuous monitoring, inspections, and testing to detect any potential issues early, ensuring the equipment functions reliably and efficiently during the enhanced oil recovery process.
Distribution and Customer Support
Finally, the equipment is distributed to customers, who may require customer support to assist them with the operation of the equipment. Overall, the development and production of geophysics equipment is a complex process that requires expertise in a wide range of fields, including electronics, physics, and software development.
Identify the Problem
The first step is to identify the key measurements necessary for optimizing enhanced oil recovery (EOR) processes, focusing on factors like reservoir conditions, fluid dynamics, and energy consumption. This enables the development of strategies that improve recovery efficiency, reduce environmental impact, and ensure compliance with safety and regulatory standards.
PAULSSON IN THE FIELD
Abu Dhabi
2007
A Large 125 level array 3D VSP Survey for ADCO in Abu Dhabi, February – April 2007


China
2007
A 160 Level 3C 3D-VSP in Daqing Oil Field, China – Four Surveys
Wyoming
2006
160 level array survey for BP. Largest onshore survey in the US as of 2006: 3 million traces. World Record.(Wamsutter Field, WY)

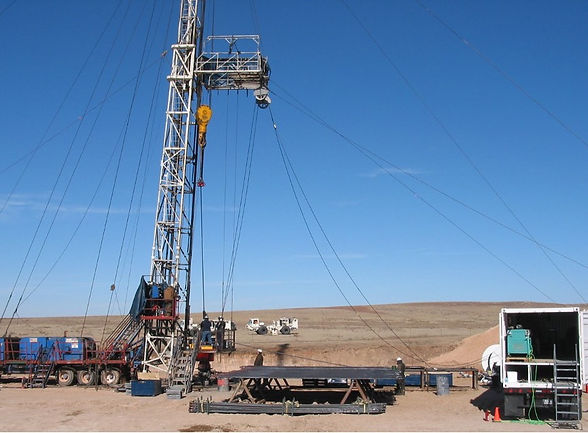